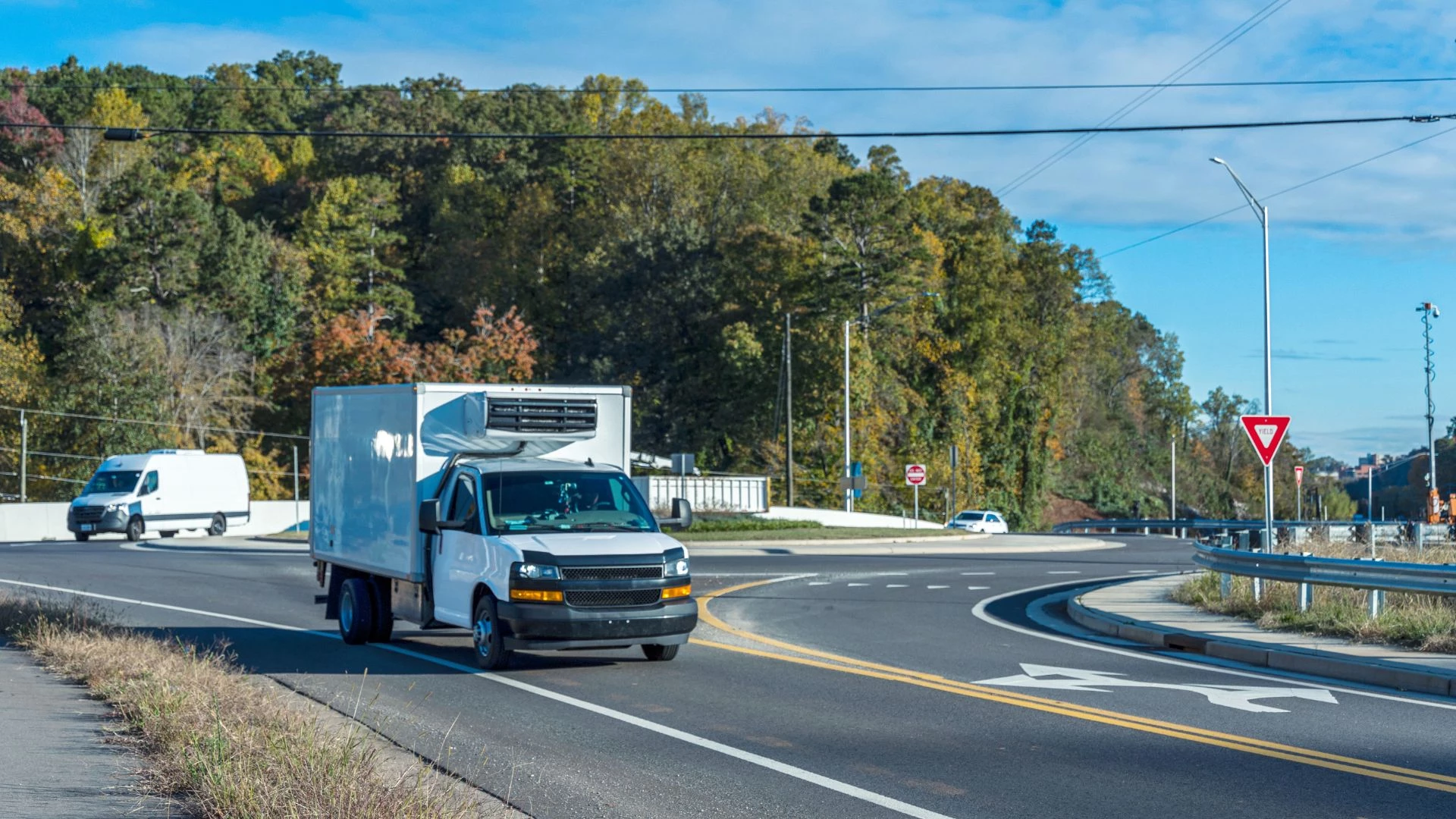
From the customer’s perspective, same-day refrigerated delivery might appear similar to regular shipping. However, it’s a complex process requiring the coordination of multiple resources, from fast pickups to advanced route planning for efficient delivery.
So, how does it work behind the scenes? Let’s step into the role of a same-day carrier to uncover the process.
You Have One Day To Do That All
Same-day refrigerated delivery ensures that perishable goods reach their destination quickly and at the correct temperature. Below is a breakdown of how it works.
Order Confirmation and Preparation
Once a deal is finalized, the process of same-day refrigerated delivery moves into action immediately. During this stage, the carrier reviews the specific details of the shipment, including the type of cargo, temperature requirements, quantity, pick-up and delivery addresses, and the urgency of the shipment.
This phase is done to choose the right vehicle with refrigeration capabilities that match the cargo’s requirements. Whether it is fresh produce, pharmaceuticals, or other perishable goods, each order demands careful temperature control to prevent spoilage during transit.
Vehicle Assignment and Pre-Cooling
Each shipment has unique temperature requirements, and selecting a vehicle equipped to meet those needs is critical. For time-sensitive deliveries, such as those within 24 hours, vehicles with efficient cooling systems and capacity suited to the cargo size are prioritized.
Before the driver arrives at the pickup location, the refrigeration unit is activated and adjusted to the exact temperature required for the cargo, whether frozen, chilled, or cool. This controlled environment reduces temperature fluctuations that could harm sensitive goods, such as dairy, pharmaceuticals, or fresh produce.
Preparing the vehicle with the correct settings in advance ensures that once loading begins, the interior is already stabilized, allowing the cargo to maintain its quality from the outset.
Advanced Route Planning
For same-day refrigerated delivery, finding the fastest and most efficient route is required to ensure that temperature-sensitive cargo reaches its destination without delay. Using real-time data, the team carefully analyzes traffic patterns, road conditions, and weather forecasts.
With perishable goods, even minor delays can compromise product quality, making route efficiency crucial. Potential roadblocks like construction zones, traffic congestion, and unexpected detours must be minimized.
Quick Pickup and Loading
With the route mapped out, the driver heads to the pickup location to begin loading. Every second matters, as exposure to external temperatures, even briefly, can affect perishable items. Drivers are trained to handle these goods carefully and load them swiftly to maintain the cold chain.
Once loading is complete, the driver verifies that the cargo is secure and that the refrigeration unit is functioning at the set temperature. With a secure load and a stable internal environment, the cargo is ready for transport.
Real-Time Monitoring
The vehicle’s location and the refrigeration unit’s temperature are constantly tracked using advanced GPS and temperature-monitoring systems. If a temperature fluctuation occurs or an unexpected delay arises, the logistics team receives an immediate alert, allowing them to take corrective action without delay.
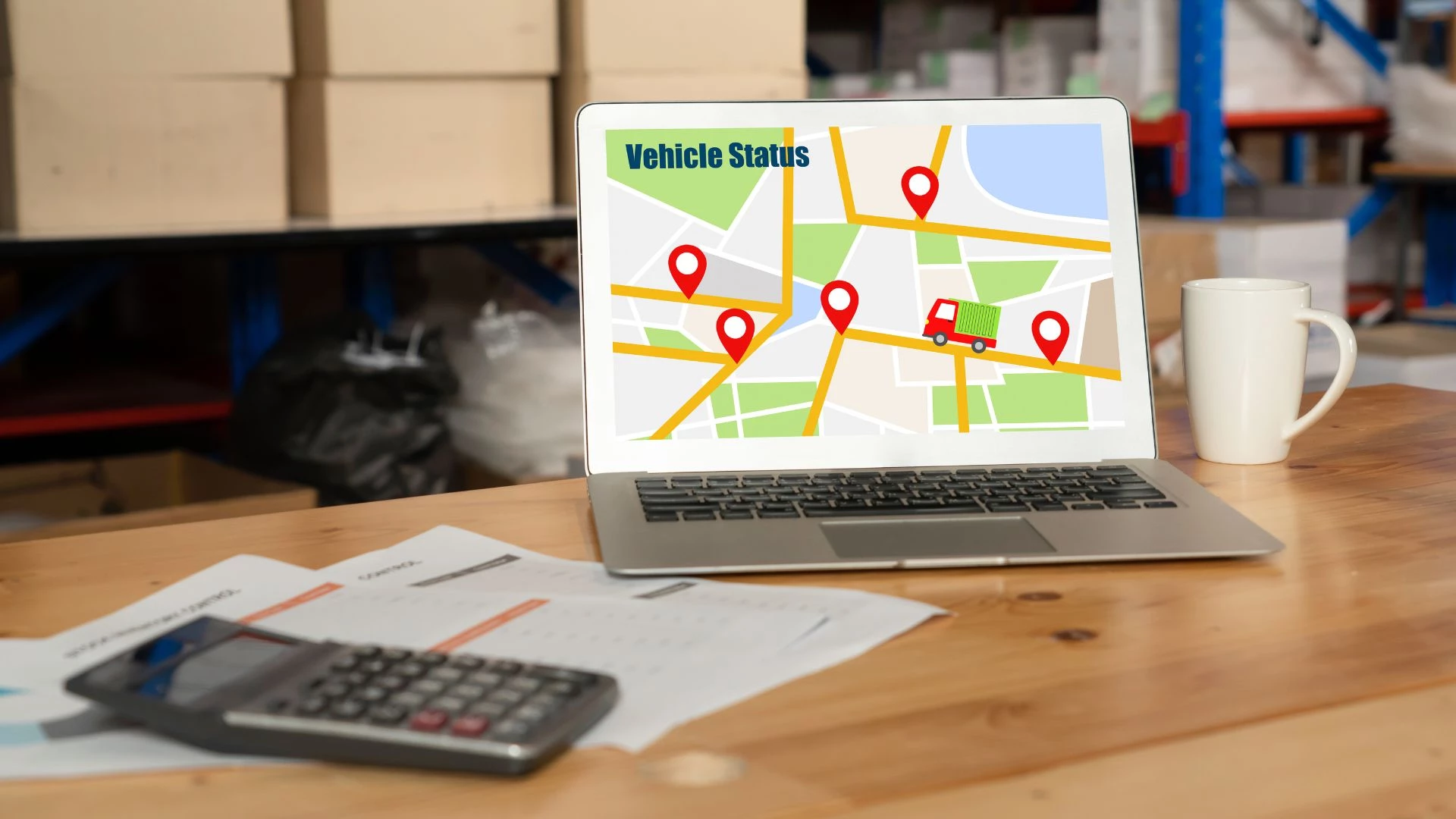
Safe Unloading
Given the urgency and temperature sensitivity, unloading is handled with speed and care, reducing the time that goods are exposed to outside conditions. Upon unloading, the receiving party typically inspects the cargo to verify its condition. Temperature-sensitive items, such as fresh produce or temperature-controlled pharmaceuticals, are checked to confirm that they have been maintained at the appropriate temperature throughout transit.
This final step is crucial in meeting customer satisfaction and preserving the reputation of same-day refrigerated delivery services.
Post-Delivery Checks and Reporting
A reliable carrier company always performs a post-delivery check to confirm that each aspect of the shipment meets quality standards. This involves reviewing temperature logs recorded throughout the journey to ensure the cargo stays within the required temperature range.
Delivery time is also reviewed to confirm that the shipment met the agreed-upon schedule. Any delays or issues encountered along the route are documented, allowing the logistics team to identify and address potential areas for improvement.
Comprehensive post-delivery reporting serves as a foundation for refining operations. By maintaining detailed records, carriers can enhance their protocols, address recurring issues, and improve the overall customer experience.
RVN’s Commitment to Excellence
At Reefer Van Network (RVN), we understand the critical importance of timing and precision when handling temperature-sensitive goods, especially for businesses that depend on consistent quality and speed. From fresh produce to pharmaceutical supplies, RVN’s high standards ensure that products reach their destination safely, on time, and at the correct temperature.
From the moment an order is placed, RVN takes rigorous steps to manage the same-day delivery logistics. Our process begins with careful vehicle assignment and pre-cooling, tailoring the transport conditions to suit each shipment’s unique temperature needs. We provide advanced route planning using real-time data to identify the fastest, most efficient paths, minimizing any potential delays and ensuring a smooth journey from start to finish.
At RVN, we use GPS and temperature-monitoring technology to oversee each delivery closely. This real-time tracking allows us to detect and respond to any temperature fluctuations or route adjustments, addressing issues promptly to protect the integrity of the cargo.
With an unwavering focus on quality, efficiency, and reliability, we stand as a trusted partner, ensuring that every shipment arrives safely, swiftly, and in optimal condition.
Back to blogYou may also be interested in
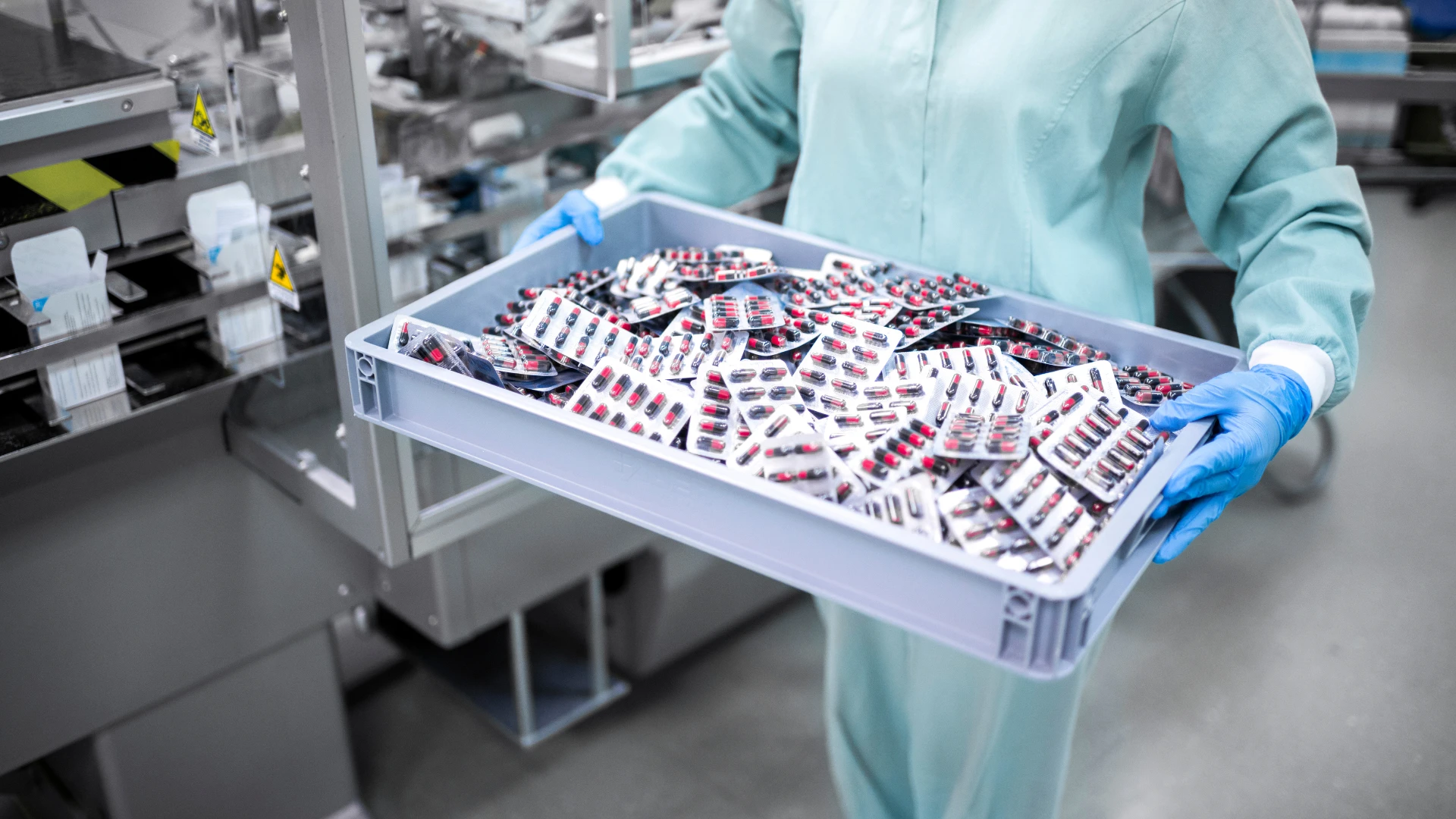
How to Tighten Pharma Logistics with On-Demand Reefer Vans
Pharmaceutical logistics is one of the most time- and temperature-sensitive segments of the supply chain. Delays, temperature excursions, or last-mile missteps can result in spoiled products, regulatory violations, and risks to patient health. As the need for agility and precision in pharma transportation grows, on-demand reefer vans are becoming a key solution. Here’s how these […]
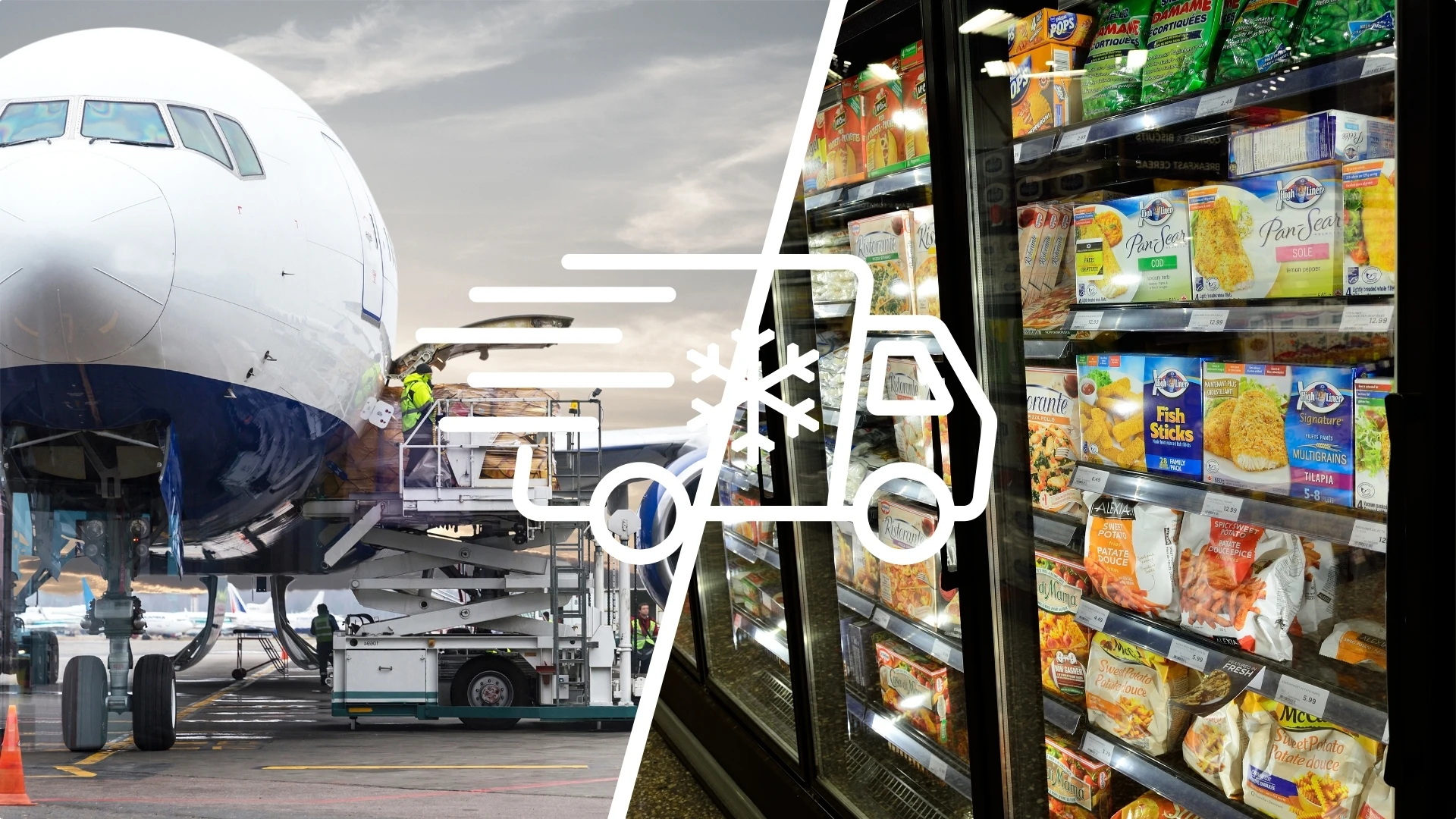
Airport to Shelf: Optimizing Short-Haul Cold Chain Logistics
When fresh strawberries arrive from Mexico, vaccines come from Europe, or seafood is imported from Asia, the cold chain doesn’t end at the airport. The most critical phase begins, delivering goods safely and quickly from airport terminals to grocery shelves, pharmacies, or restaurants. This short-haul leg, often less than 100 miles, is where timing, temperature […]