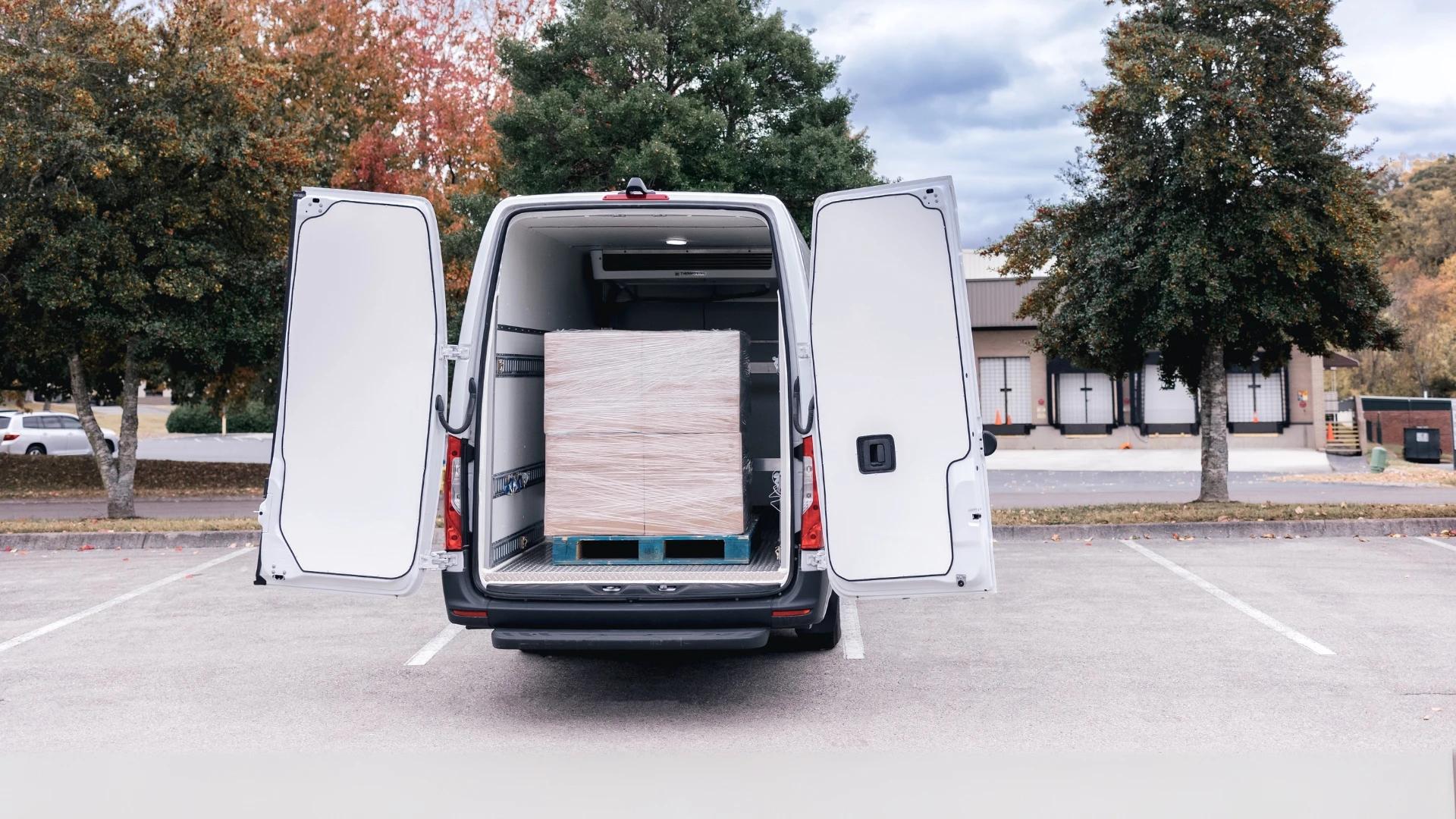
Mistakes in packing and transporting temperature-sensitive and time-critical goods can lead to a loss of brand reputation and customer trust, not to mention financial losses. Businesses in the food and beverage, pharmaceutical, cosmetics, and other industries that rely on cold-chain logistics understand this better than anyone else, considering proper packaging preparation critical to the delivery process.
This step-by-step guide to packing and transporting refrigerated goods is designed specifically for them. It aims to help recap the main packing and transportation rules to keep temperature-sensitive shipments in top condition from the warehouse to the final destination.
The Basics of Cold Chain Logistics
Cold chain logistics is all about transporting and storing products in a temperature-controlled environment. Cold shipments generally fall into two categories – chilled and frozen. The first one includes goods, like vaccines, which must stay between 2–8°C, whereas the frozen category covers items like meat or ice cream that require 18°C or lower. Despite the differences, products under both categories have specific temperature and humidity requirements, so a well-maintained cold chain is always critical.
Step 1 – Assessing Your Product Requirements
Every temperature-sensitive product has unique needs, so the first step is to identify the exact storage conditions it requires during transit:
- Storage Temperature: Determine the optimal temperature range for each product. Dairy products typically need 2–4°C, while frozen meats must stay at -18°C or below. For medical shipments, the CDC’s Vaccine Storage & Handling Toolkit provides authoritative temperature guidance.
- Humidity and Airflow: Check if your goods need specific humidity or ventilation. Fresh produce and flowers often need moisture to prevent drying out, whereas other items require a dry environment to avoid condensation or freezer burn. Ensure your packaging allows a bit of airflow for even cooling.
Step 2 – Preparing Packaging
After determining your product requirements, gather the right packaging materials to maintain those conditions. High-quality packaging is your first line of defense against temperature fluctuations:
- Insulated Containers: Use insulated containers (like foam boxes or thermal blankets) to keep heat out. Choose a container size that minimizes empty space and helps maintain the target temperature.
- Cooling Agents: Use gel packs for chilled goods and dry ice or frozen gel bricks for frozen goods. Add enough coolant to last the journey (or plan a mid-transit top-up for very long trips), and handle coolants safely.
- Packing Configuration: Pack items to maximize cooling efficiency. Place cold packs strategically (usually on top and around the products) and fill any voids with insulating material. Keep everything snug so nothing shifts.
- Packaging Quality and Sustainability: Opt for eco-friendly materials like recyclable liners or reusable ice packs to reduce waste – customers appreciate green initiatives.
Step 3 – Selecting a Transport Mode and Partner
Before sending your refrigerated goods on their journey, choose the transportation services that best suit your shipment size, distance, and required speed. Reefer trucks and vans are ideal for precise temperature control and often come equipped with onboard monitoring systems to track conditions. When deciding between air freight and ground transport, weigh factors like cost, travel time, and how reliably you can maintain your cold chain. Quick local deliveries usually involve shorter packing durations and lower risk of temperature fluctuations, while longer, cross-country shipments call for more robust cooling methods and possibly mid-transit interventions.
When evaluating carriers, research their experience and track record. A reliable, time-tested partner like Reefer Van Network, with a modern reefer fleet, real-time tracking, and knowledge, will provide professional guidance throughout the entire journey.
Step 4 – Loading and Handling
Once you’ve locked in the right mode of refrigerated transportation, it’s time to focus on loading and handling procedures. Pre-cool the vehicle to the proper temperature before loading any items, ensuring that your goods maintain consistent conditions from the start. Arrange pallets and boxes in a sequence that places the most temperature-sensitive goods in optimal positions, usually away from doorways and in the coldest zones.
During the loading process, minimize the number of times the truck or van doors open to prevent temperature spikes. Goods should be secured to avoid shifting, which could compromise insulation or crush packaging. Also, never mix products that might cross-contaminate one another.
Step 5 – Monitoring During Transit
Real-time temperature tracking is vital to catch any potential dips or spikes before they become a problem. Many shippers use IoT sensors or onboard monitoring to keep an eye on the cargo environment throughout the journey. If something goes awry, a contingency plan should be readily available.
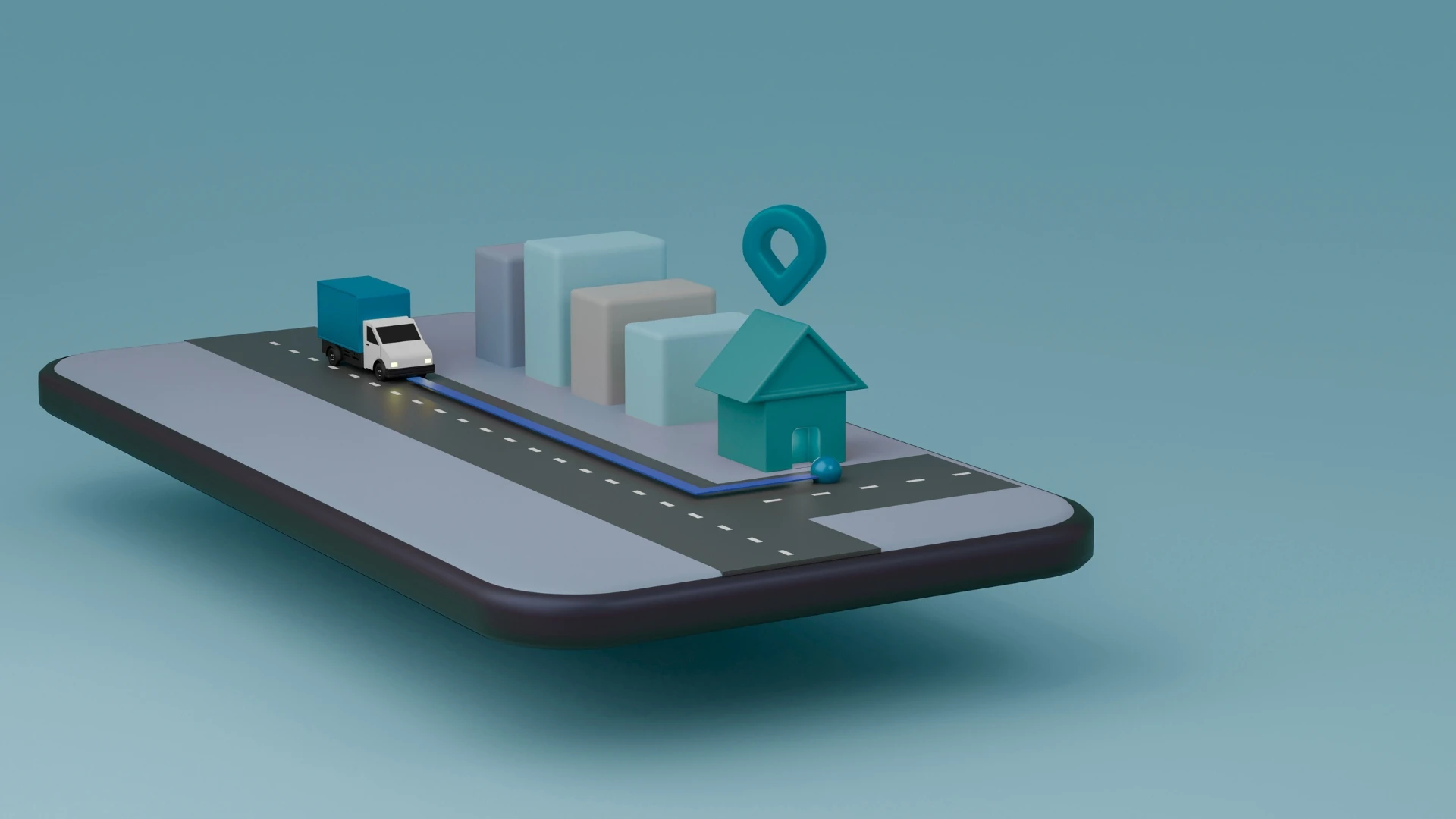
Step 6 – Receiving and Storage Upon Arrival
Unload your cargo promptly to reduce exposure to outside temperatures. Even short delays on a loading dock can sabotage a perfectly maintained shipment. Inspection and verification should follow immediately: compare temperature logs against predetermined standards, check for any breaches in packaging, and quickly note any discrepancies.
After confirming the shipment’s integrity, move it straight into the appropriate cold storage facilities. Depending on your product type and regulatory requirements, you may need to document each stage of the handover for compliance.
Tips for Cost Efficiency
Good packaging and cold-chain transportation don’t have to be expensive if you follow several simple tips. Optimize load sizes to fill reefer vehicles without compromising airflow or safety. Next, plan routes carefully to avoid unnecessary detours that can raise fuel costs and risk temperature swings. Finally, consider using smart packaging with sensors that track temperature in real time, allowing for quick adjustments.
Common Pitfalls to Avoid
Many issues in the cold chain arise from small oversights that spiral into big problems. Inadequate insulation or a poorly sealed container can cause rapid temperature spikes, ruining entire shipments. Neglecting to secure proper insurance might save pennies initially, but it becomes a nightmare if a breakdown leads to spoiled goods. Also, don’t underestimate the risk of subpar carriers – companies lacking modern fleets and robust temperature controls can jeopardize both product quality and regulatory compliance.
Summary
The effective packing and transporting of perishable goods requires attention to every link in the cold chain, from product selection and packaging to choosing the right transportation services and verifying final delivery. Equally important is choosing a trusted partner like Reefer Van Network to help navigate all the complexities while minimizing risks.
Back to blogYou may also be interested in
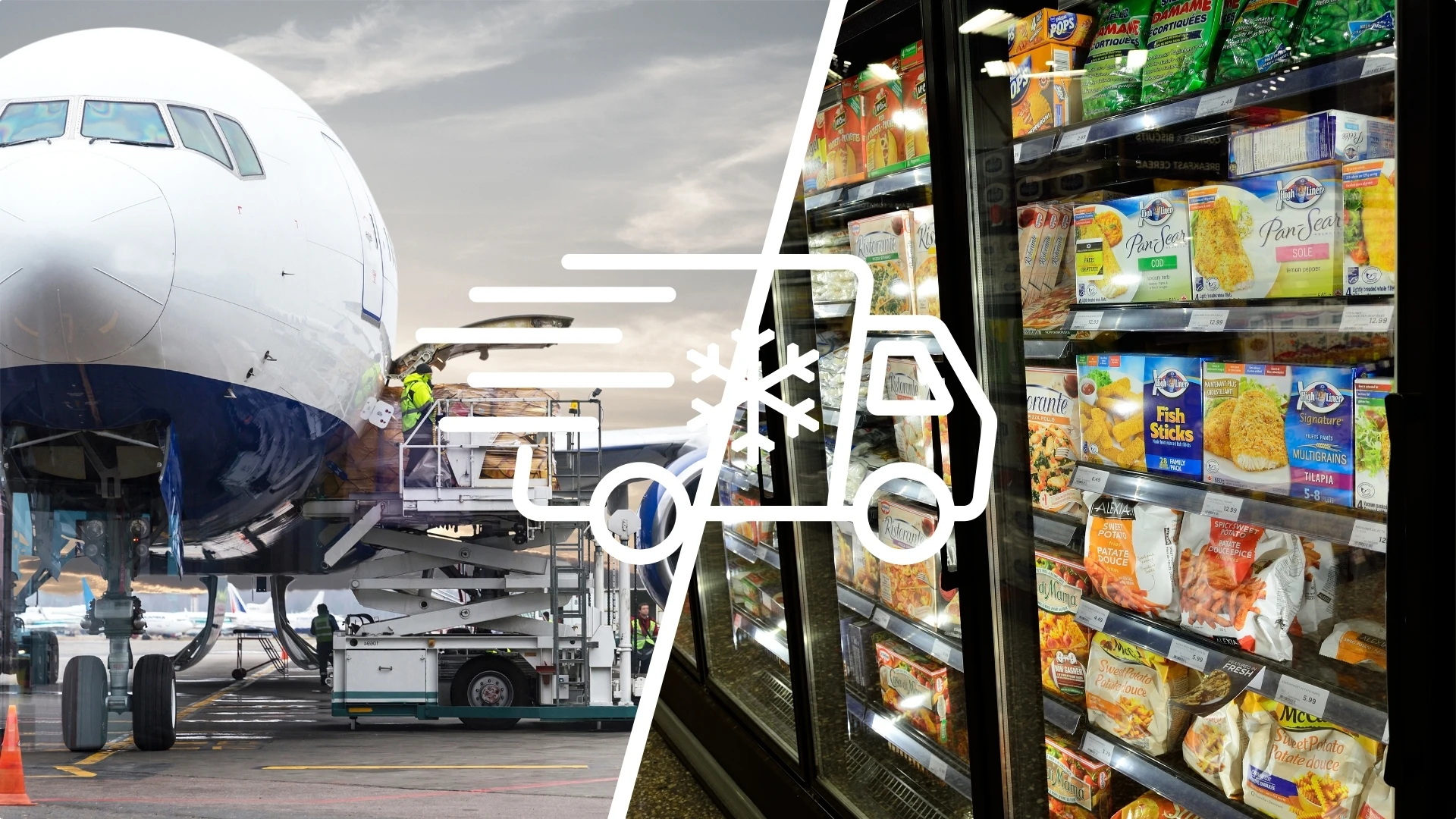
Airport to Shelf: Optimizing Short-Haul Cold Chain Logistics
When fresh strawberries arrive from Mexico, vaccines come from Europe, or seafood is imported from Asia, the cold chain doesn’t end at the airport. The most critical phase begins, delivering goods safely and quickly from airport terminals to grocery shelves, pharmacies, or restaurants. This short-haul leg, often less than 100 miles, is where timing, temperature […]
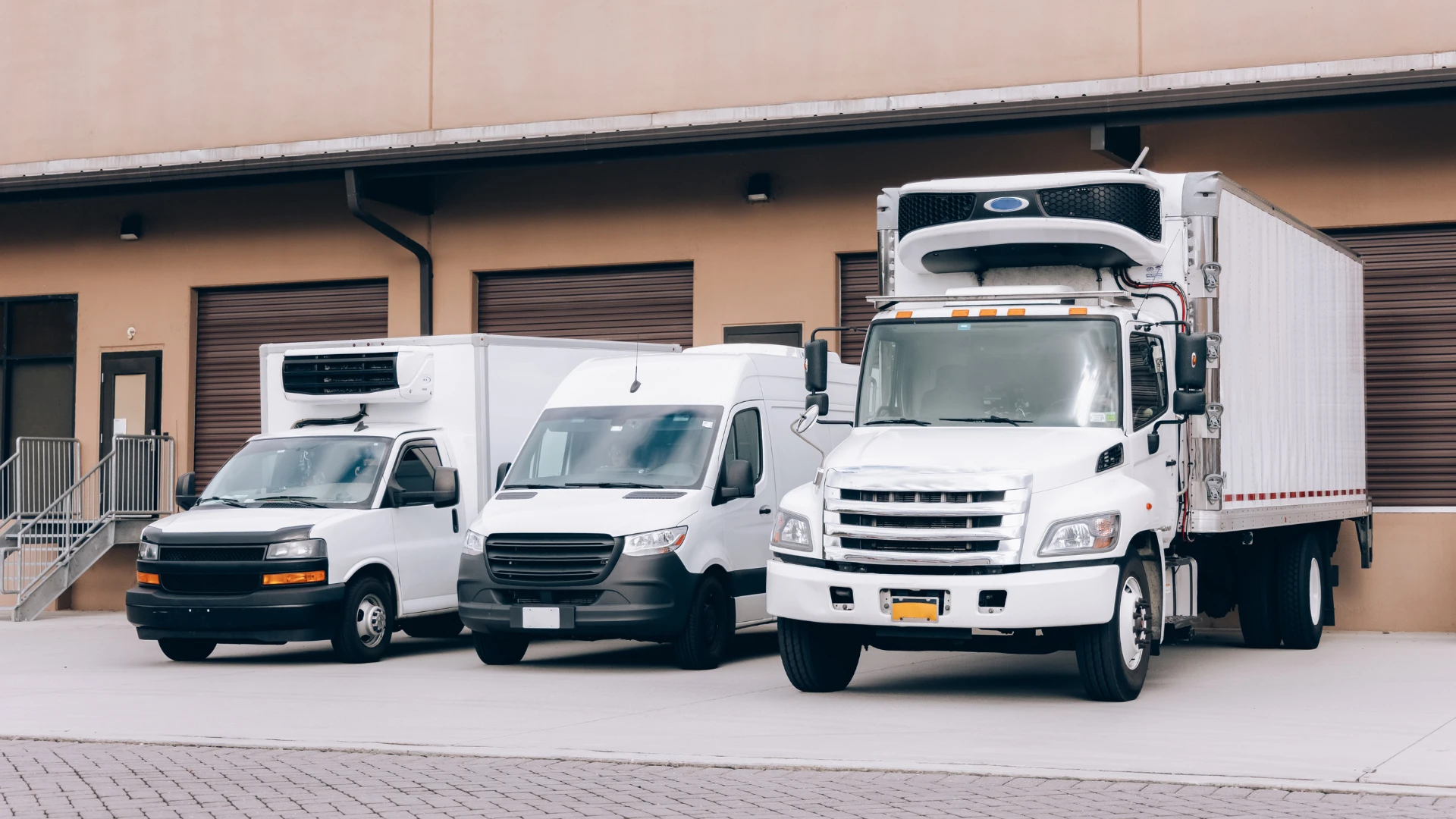
No Trucks, No Trust: Why Chain Brokers Need Capacity on Standby
In the world of cold chain logistics, timing and temperature are everything. Delays don’t just result in missed appointments; they result in spoiled goods, broken supply chains, and lost clients. For chain brokers, having standby capacity, refrigerated trucks available at a moment’s notice, is no longer a competitive edge. It’s a baseline requirement. Imagine this: […]